Introduction to Air Cooled Heat Exchangers (ACHE)
ACHE’s are used to cool liquids or condense gas to liquid. ACHE comprise of a bundle of tubes and fans.
The warm liquid is pumped through the ACHE tubes and the heat is rejected by blowing cooler air across the outside of the tubes.
ACHE is used in a vast array of industries from large scale condensers in power stations to very small coolers on an oil closed loop system.
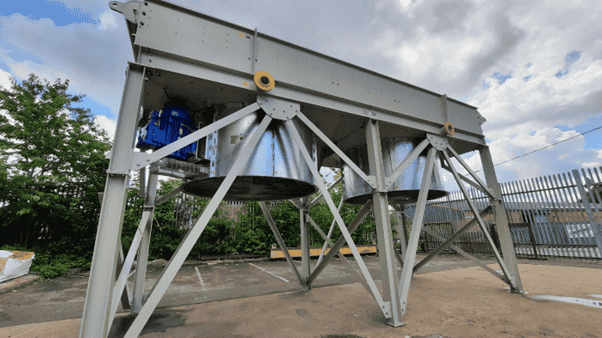
Other names given to Air Cooled Heat Exchangers
- Dry Coolers
- Finned Tube Air Exchangers
- Seal Cooler
- Air Blast Coolers
- Air Cooler
- ACHE
- Fin Fan Coolers
- Heat Exchanger
- Air Exchangers
Industries and Applications for ACHE
- Industries
- Oil and Gas
- Petrochemical
- Food and Beveridge
- Nuclear
- Marine
- Renewable
- Power Generation
- Pulp and Paper
- Hydrogen
- Carbon Capture and Storage
- Data centres
- Electrical
- Sugar
- Wind Power
- Tidal Power
- Tobacco
- Automotive
- Steel
- Process Liquids and Applications
- Condensers
- Gas
- Liquid
- Hydrocarbons
- Lubricating Oil
- Hydraulic Oil
- GazPaks
- Purge Air
- Water
- Steam
- Inter cooler
- After cooler
- Seal Air
- Seal Fluids
- Vacuum Steam Condensers
- Flue Gas
- Economisers
- Hydrogen
- Machines and Plant
- Gas Turbines
- Pumps
- Compressors
- Engines
- Cars
- Trucks
- Transformers
- Exhausts
- Flue Stacks
- Data Centres
- Mills
- Refinery
- Seal Systems
- Factories
- Buildings
- Hospitals
- Shopping Centres
- Ships
Why Select ACHE?
ACHE are a favourable solution when cooling water supply is limited or of poor quality. Shell and Tube Heat Exchangers are more commonplace and tend to be a cheaper to install but more expensive to operate. Air cooling offers distinct advantages that outweigh the initial benefits of other types of cooling.
- No water consumption. ACHE relies on moving air over the tube block to cool the process liquid inside flowing inside the tubes.
- Simpler Control: ACHE are controlled simply by adjusting the motor speed or louver position (if fitted) or fan running periods.
- Maintenance: ACHE are reliable and designed to last ~25 years in continuous service. Tubes can be inspected, plugged or replaced easily. Fans and motors are also accessible. Air coolers do not suffer from water fouling and corrosion issues that commonly arise with other types of coolers.
- Risk of leaks: ACHE leaks are rare but can normally be fixed quite easily. Leaks do not cause a contamination with the process liquid unlike other heat exchangers which use liquid-to-liquid cooling. (If a shell and tube leak occurs water may get into the oil and cause serious damage to the plant)
- Ambient air: A good differential temperature is required between the warm liquid and the cooler air to ensure the unit can be sized sensibly. It is recommended that at least 10° ‘delta T’ between ‘air on’ temperature and liquid outlet temperature is considered.
- Water availability: ACHE are likely to be selected when cooling water is in low supply. OR in arid locations where water requires extensive treatment to reduce fouling in a shell and tube design.
- Plot space: ACHE can be larger than other heat exchanger solutions but require less piping and pumping infrastructure than the alternatives.
- Piping complexity: ACHE may need to be split into banks side by side and these banks may need piping together. However, the piping is simpler than other Exchangers which may have a heating process and a cooling process line to consider too. (ACHE don’t need cooling nozzles because it is using ambient air)
- CAPEX/OPEX: ACHE is normally higher in price to other heat exchanger systems. But the OPEX is usually less. The fans motors are cheaper to run than cooling water pumps and maintenance costs are far less due to the low risk of corrosion issues. ACHE suppliers may offer different kW motors depending on the thermal design of the unit, this can vary from supplier to supplier.
- Effluent: ACHE do not produce any effluent and are therefore more likely to comply with government regulations as they do not discharge water to the environment.
Design Process
The supplier of ACHE will utilise thermal design calculations to reach the best design for each unit. There are many variables that need to be considered before the most suitable and efficient design is reached. For example: tube type, materials, tube length, number of tube rows, tube pass arrangement, fan selection, ambient conditions, environmental conditions, seasonal changes, air quality, process boundary conditions, electrical power supply and more.
In most cases the client or end user will set out of the design parameters in a datasheet format to help the supplier start the thermal and mechanical design.
The most competent suppliers will use commercially available design software such as HTRI or ASPENTech and this may be enhanced with inhouse design tools too.
To maximise the heat rejection in the smallest possible footprint the designer of the ACHE will select tubes that have external fins and/or an internal tube insert turbulator. The external tube fins help the heat transfer by adding surface area. The tubulator helps heat transfer of viscous fluids by disturbing the laminar flow creating turbulence in the fluid flow. The designer will maximize the internal and external tube surfaces to ensure the most economical design also with full consideration to the fluid properties and allowable pressure drop.
Some suppliers can also offer very high-performance bonded tube inserts. These are soldered inside the tube to provide both: turbulence and heat conduction. Bonded inserts are not currently covered by commercial design software such as HTRI or ASPENTech but can greatly increase the thermal heat transfer. For example, a bonded insert can enable 6 times more heat transfer than a twisted strip insert.
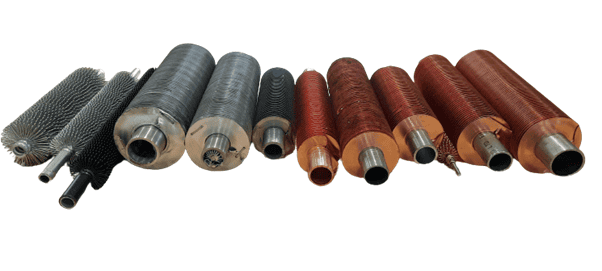
The designer also selects the most appropriate motor and fan to give good air flow across the tubes. API 661 sets out clear guidelines on the best practices for the fan and tube block sizing. There needs to be certain geometry observed to ensure that the flow of air reaches all of the tubes.
Fan Selection
Normally the ACHE supplier will purchase fans from a fan specialist who will support in the correct selection for the application. The Fans are housed in a fan casing. ACHE are either forced draft or Induced Draft, each have their advantages and disadvantages.
The fan may either be driven by an electric motor or a shaft drive from an existing machine. A Belt and pulley can be used to reduce the speed of the fan blades to give the desired air flow.
The Fan selected should provide the required air flow comfortably at normal ambient conditions with good margin either way (on the fan curve) to ensure the fan is not running at it top or bottom range condition. The fan angle should also be set in a middle range position by design so that the blade angle could be adjusted during commissioning for optimum air flow and noise. The fan blade tip speed can generate excessive noise if it is too high which also needs to be checked during the factory acceptance test (FAT).
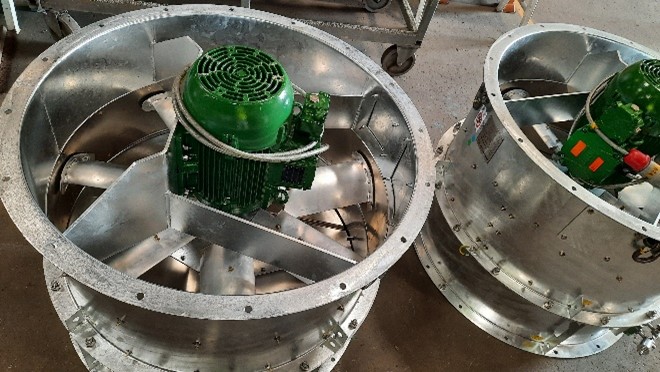
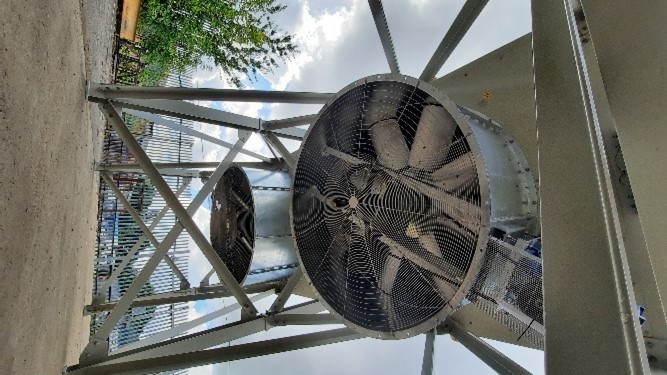
Mechanical Design
Once the thermal design is complete some of the key design parameters are set such as: tube length, tube rows, fan size, qty of fans etc. The wall thickness of the tubes and header plates is established to ensure the pressure parts can withstand the design pressure at the design temperature.
Header design can vary depending on the client’s preference, maintenance access and size of the units. Simple designs may use standard pipe or box section as the header with holes drilled for the tubes to penetrate. Or larger ACHE tube blocks may use headers fabricated from plate with threaded plugs for accessing each tube, or alternatively simple ‘D’ shaped headers formed from half a pipe welded to a tubesheet.
Detailed Design
Once the thermal and mechanical designs are completed a draftsman will undertake the full and detailed layout of the cooler. Normally a General Arrangement drawing is produced first with all the major outline dimensions, nozzle locations, foundation loads, key design data present. Once the GA has been thoroughly checked and approved the detailed fabrication drawings are developed.
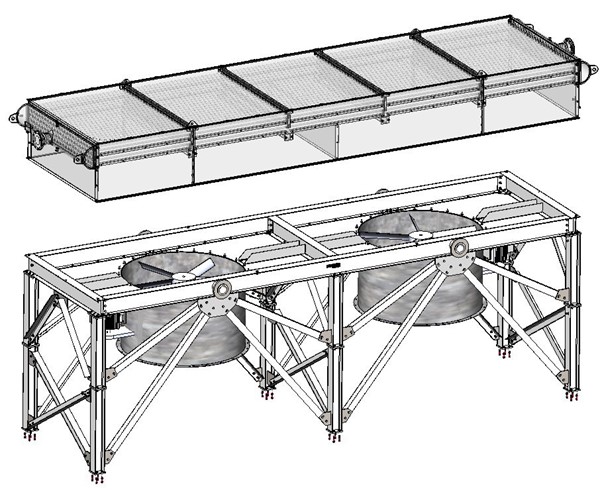
Purchasing
The ACHE vendor will have their own established supply chain for all the bought in items and materials. Also, the end user may have restrictions on the permitted materials or an Approved Vendor List (AVL) to be followed.
The purchaser will ensure that all the client specifications are met by the sub-suppliers.
Longer lead time items are purchased first. Normally this is the fan and motor. Motors can be long lead times especially if it must be rated for a hazardous area and/or comply with onerous specifications. Often the lead time for the ACHE is dictated by this as the critical path.
ASME and PED projects require specific record keeping and material certificates need to be provided and full traceability from the certificates to the material markings (heat number) is required to comply with the code.
All other materials are purchased in accordance with the design Bill of Materials and are scheduled to arrive in time for production.
Manufacturing
The tubes are inserted and finned according to the design. Finning could be extruded, embedded G fin, L fin or LL fin.
Tube inserts may be ‘pull in’ type made from wire mesh or twisted strip; OR they could be higher performance bonded turbulator where the insert is soldered to the inside of the tube. Bonded inserts are only manufactured by the most experienced tube suppliers.
The Tube Block assembly is governed by the pressure part design code in the destination county for the unit. Normally PED for Europe or ASME for the rest of the world.
Tube sheets are precision CNC milled to achieve tight tolerance of the hole to the tube OD.
Plug header from plates are also CNC machines and threaded to allow plugs to be screwed in and sealed with a special flat washer. The plugs are machines and threaded from solid bar stock material.
Tube block welding is performed by qualified coded welders who are regularly tested for having suitable skill level for the welding process required. Nozzle are full penetration butt welded.
Tubes can be expanded into the tubesheet or welded.
Once the tube block is finished it would normally be air leak tested underwater, hydrotested above the design pressure, flushed and dried.
The carbon steel items should be painted or galvanised.
The distance from the tip of the fan blades to the fan casing should be checked and controlled.
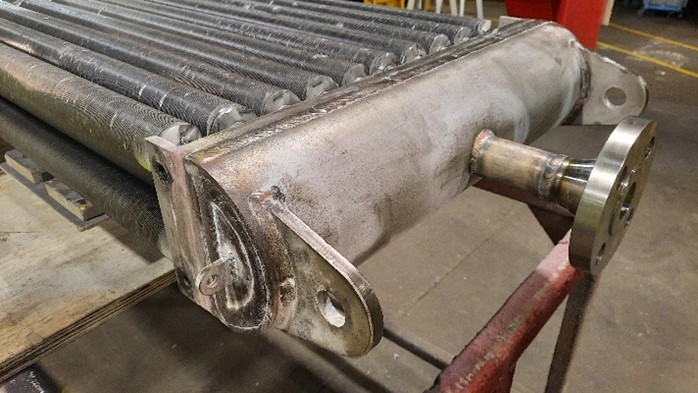
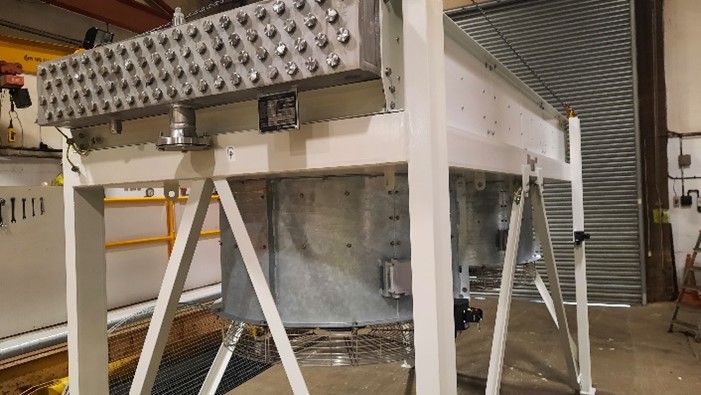
NDE / NDT
Each ACHE has an Inspection and Test Plan which plans all the required inspection points when they should be conducted and what the acceptance criteria is.
The following is typical:
PMI of materials, Radiography of welds, Dye Penetrant testing of welds, Dry Film Thickness checking of paint, Visual Dimensional Inspection, Fan Run Test, Noise Test, Vibration Test, Filter check during vibration flushing, Hydrotest, Air Leak Test.
The following 3rd parties may also be required to attend Lloyds, DMV, NACE etc as well as the clients representative.
Pickling and Passivation is required on the welds if stainless steel.
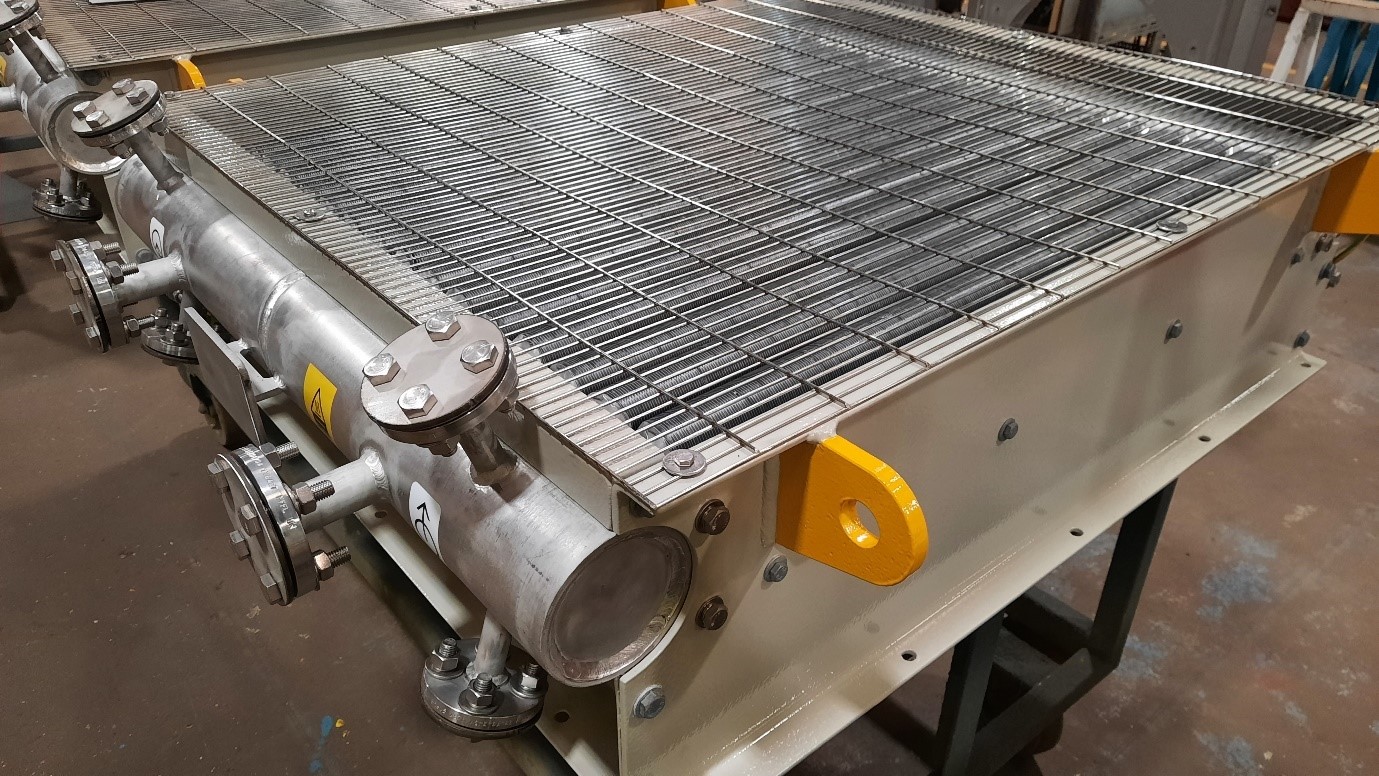
Summary
ACHE is a versatile Heat Exchanger that can very easily cool a process simply by using ambient air. It does not require water or a coolant supply, just air. Its simplicity and reliability mean that it is used commonly for many industrial applications. Good design will result in a compact unit that will run continuously for many years with minimal maintenance and running costs. There is zero effluent discharge and don’t normally suffer from fouling or corrosion issues. ACHE designers achieve low electrical power consumption by providing an efficient design that maximises the tube technology available. Tubes can be finned externally and have internal inserts to turbulate the fluid flow. Heat transfer can be enhanced further by using high performance bonded tube inserts. Accomplished suppliers of ACHE will have several specialist departments set up to ensure quality of design, material and production is maintained at all stages and the final product is guaranteed as suitable for is application by rigorous inspections and testing prior to delivery to the end user.
Vendor Selection
Specialist Heat Exchangers Limited (SHE) are an excellent choice of supplier for the following reasons:
- SHE can offer bonded tube inserts which can perform 6 times better than pull in inserts for viscous process fluids, such as oil.
- SHE uses in-house proprietary design software in addition to HTRI to guarantee the process cooling and allow selection of tubes with bonded inserts.
- SHE has refined their design and manufacturing of ACHE, building every day on experience since year 1968 with 1000’s of operational coolers commissioned successfully around the world. SHE has developed the best-in-class procedures to deliver high quality ACHE’s.
- SHE fin their own tube to a high standard using propriety HERCOL tube finning machines with positive collet and chuck drive mechanism which give superior fin attachment for all L, LL and G fin tube.
- SHE can certify units to ASME and PED and Hydrotest up to 500bar(G) to ensure pressure parts are fully safe prior to service.
- SHE specialises in ACHE and so focus on this product as their core product.
- SHE design and manufacture in the UK in Lincoln city.
- SHE hold ISO 9001, 14001 and working towards 45001 and 27001.
- SHE hold ESG policy aligned with government initiatives to achieve net zero 0 by 2050.
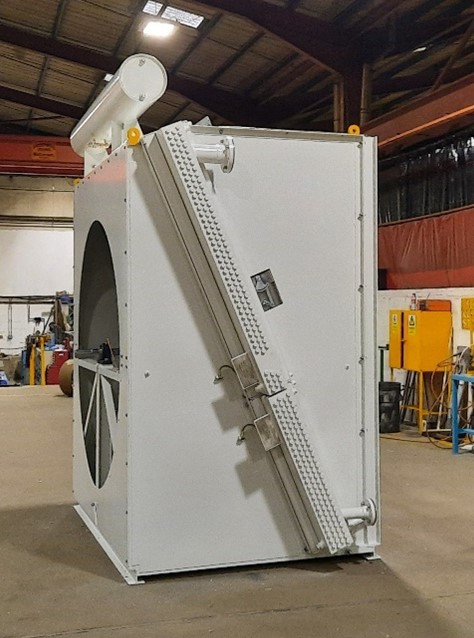
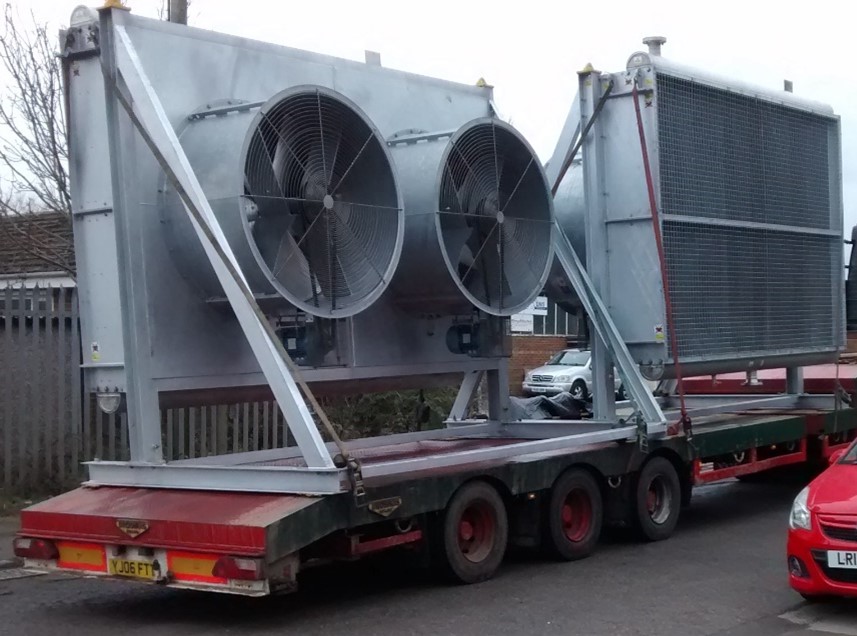